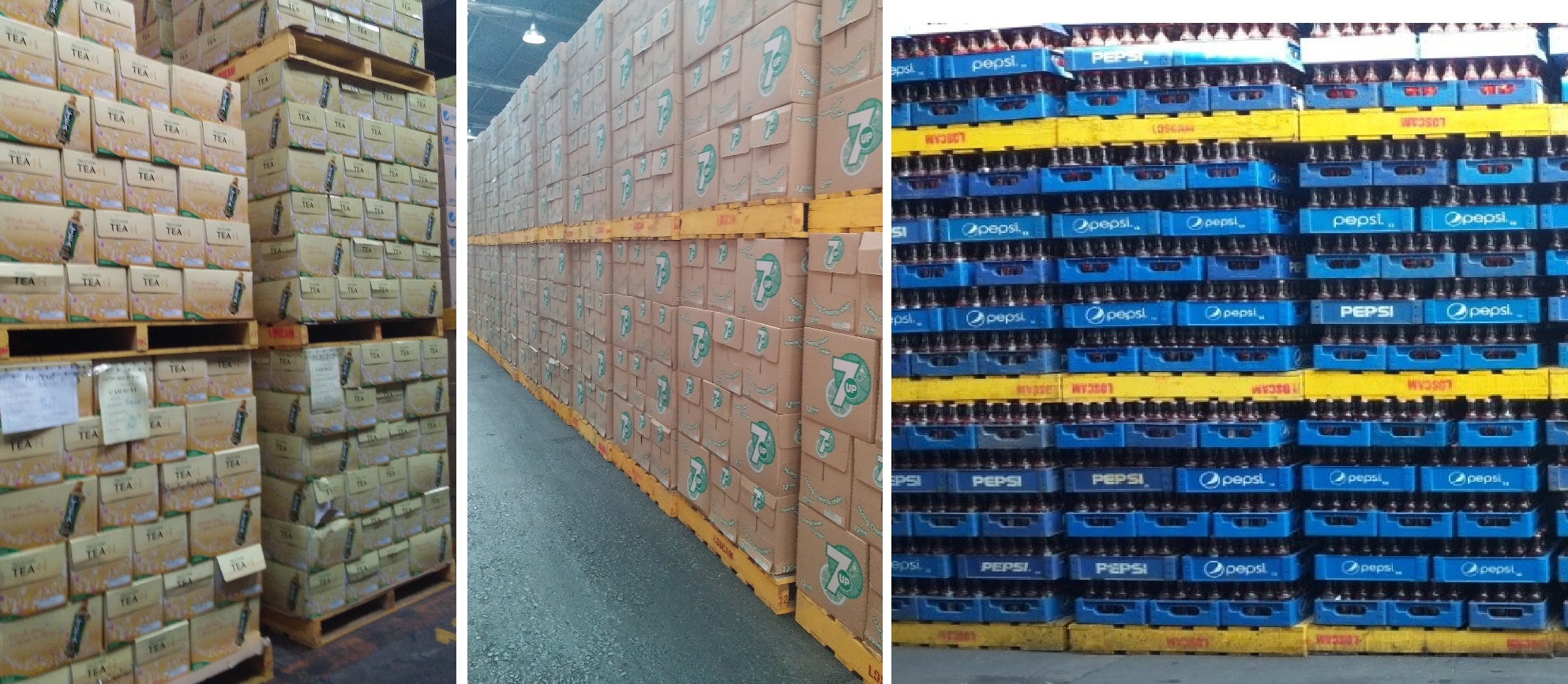
Loscam Vietnam revealed the team's effort in offering a switch to standard pallets and Loscam's web-based equipment control system has brought benefits for Vietnam's largest beverage business. The situation was becoming challenging for one of Vietnam's biggest beverage and food brands. As the business enjoyed success and growth and its distribution network naturally widened, those challenges began to mount.
Managing the 200,000 pallets required to transport the company's food and beverage products to more than 2,000 retailers and wholesalers across the country was becoming increasingly complex and costly.
Under the Lens
The business bought its own pallets to ensure products reached customers and consumers on time and in good condition, but pallet movement and the high costs associated with repairing pallets became a key issue.
The business also experienced a fluctuation in the demand for pallets – during low season there was a glut of pallets that required additional warehouse space for safe storage. Managing and tracking the 200,000 pallets was also a logistical challenge.
In addition, the varying size and specifications of the self-purchased pallets were causing delivery problems for the brand. The pallets didn't always conform to the standardised pallets that are more widely accepted in Asia's FMCG industry. As a result, the food and beverage company found goods sometimes had to be delivered in loose cases and this increased labour costs as products had to be stacked manually. This in turn slowed the distribution process and also led to more damaged goods.
The company recognised that palletised delivery is increasingly important and dominant in Asia's FMCG industry and that it was vital to step up its performance in this area.
Transitions from Loscam's Total Solutions
Loscam has worked with the brand to implement a pallet pooling system to tackle these challenges. Before implementation, Loscam worked with senior management and operations staff to identify all pallet-related issues and to develop a transition process that minimised the impact on day-to-day production and operations. Specialised training on pallet management and control was provided to all relevant staff and to its major distributors.
Loscam's web-based equipment control system, Loscam Online, helps monitor pallet control. When empty pallets are returned, Loscam sorts and repairs them and reissues the refurbished pallets to start the pooling process again.
Loscam's pallets are also ECR standard so they are widely accepted in Asia and by the majority of the company's trading partners. This has made pallet movements more efficient and streamlined and allows the brand to manage increasingly sophisticated supply chain models.
Outcome: A Complete Transformation
The benefits for the brand have been numerous – better use of capital and resources, significant cost savings, greater efficiencies in pallet pooling, time savings in terms of a switch from manual loading to machine loading of pallets, less damage to products during transportation, and greater customer satisfaction.
The brand has introduced Loscam's pallets in North and South Vietnam and is now scaling up and rolling out the pallets to other strategic regions with the aim of full implementation of pallet pooling across Vietnam.
